Read more about our products on our blog designed specifically for you.
Pallet Flow Racking
The roller line is tilted at a certain angle and fixed on the shelf beam, the tray is put from the high end, along the roller line itself neutral slippery, to control the tray to stabilize the speed of decline, to avoid the impact of the drum line set a set of damping system, The faster the pallet is down, the greater the resistance of the damping system. The end separation mechanism is provided at the lower end for separating the two adjacent trays at the lowest end so that the lowermost tray can be smoothly removed. Gravity shelves require heavier trays, and the use of wooden pallets is already ripe. Other material pallets need to provide practical pallets for damping experiments. Gravity shelf space utilization to achieve a "first in first out" principle, safety and operational efficiency are the same with the through-type shelves, widely used in various industries.
Pallet flow racking structure features:
(1) and through, shuttle the same amount of storage capacity, the use of gravity shipments, forklifts do not have access to the channel, access more convenient;
(2) for a large number of storage and short-term shipment of goods, suitable for production and delivery needs to be done, advanced goods first out of the library;
(3) the use of dense flow storage stack stack, space utilization rate of up to 85%;
(4) the requirements of the tray is high, to ensure that the bottom can slide on the roller, each channel generally store a product;
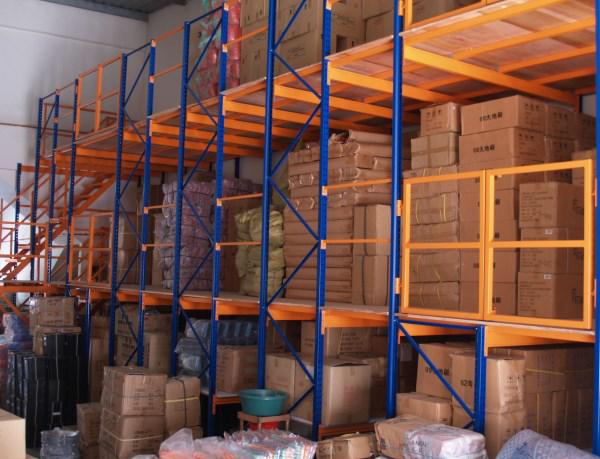
Follow the principles in the shelf design process
1, considering the weight distribution of goods caused by deformation, stacking machine or forklift movements caused by lateral momentum, seismic intensity fortification;
2, between the goods, between the goods and the shelves, as well as between the cargo and the fire-fighting pipeline to leave a safe distance, leaving out the fire spray space;
3, the selection of high-quality steel, surface rust and decorative treatment, in order to ensure the use of the performance of the premise, to minimize the cost of the project.
Shelf design should also focus on the following points:
1. The design of shelf structure, should consider the use of requirements, equipment, load properties, material supply and installation conditions and other factors, reasonable choice of structural form, structural measures and production materials, to achieve advanced technology, economic and reasonable, safe application, to ensure quality.
2. The dimensional tolerances, deformations and clearances of the shelves shall conform to the relevant standards.
3. There are strict design procedures, regardless of the durability limit state or the maximum load limit state design shelf structure, must conform to the relevant standards, must have the calculation book. For major projects must be calculated by finite element, the strength of the shelves, stiffness and stability of the composite, the earthquake under the safety of a comprehensive assessment. For repeated use of standard shelves, there must be a general-purpose calculation.
4. The data used must be based on or tested. Shelf structure is often difficult to accurately analyze theoretically, it is necessary to use the corresponding tests to determine the design parameters required, but also directly through the test to determine the shelf structure or the carrying capacity of a component. Test should be reported, the test equipment should be recognized by the state qualified measurement Department calibration, inspection qualified.
5. Cross-beam shelves, each end of the beam must be equipped with a locking device, or to provide screws and nuts fastening, so that the beam can be stably fixed on the column, to prevent the upward force from the detachment. To ensure that the beam and its locking device (or screws and nuts) of the joint, in use should regularly check the normal operation of the crossbeam lock or screw nut fastening, timely replacement of the damaged device.
6. Rack column pins should be properly fixed on the concrete foundation. To make sure that the connection between the shelves and the ground is the use of embedded parts, the use of two irrigation programs, or the use of chemical bolts and ground directly connected to the scheme. The diameter and the minimum size of the bolt must be determined by calculation according to the actual load, seismic load or wind load. 2.4m below manual feeding small shelves are not fixed. Fixed Shelf Column foundation of concrete must be cured continuously for 28 days, and withstand the corresponding pressure, the foundation of uneven settlement to meet the use requirements.
7. The settlement value of the rack-shelf base should be strictly controlled to ensure the normal use of the shelf structure. Non-Library shelves in the design should pay attention to the shelf base and building the separation of the foundation, to prevent the shelf structure of the force caused damage to the building.
8. One or more permanent signs must be placed in the eye-catching place of the shelf, the area of each sign should not be less than 20x20 (CM2), the label should be marked with a clear font of the maximum unit load (kg), each layer of the maximum uniform load (kg), the number of units allowed to be stored in each cell.
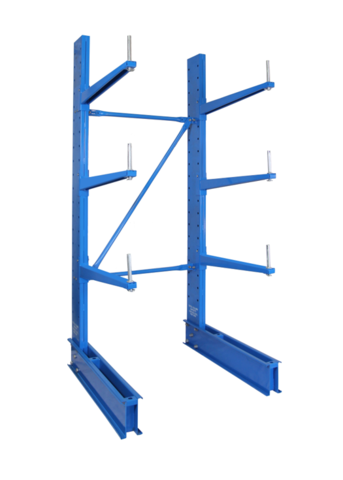
Cantilever rack is an important kind of shelf.
Cantilever shelves are suitable for storing long materials, ring materials, plates, pipes and other materials that can not be used for pallet containers. Can be single or double, with a stable structure, good load capacity, high space utilization characteristics, with the need to match the fork side of the larger side of the forklift use.
We use the column and beam plug combination, easy installation, easy to remove, easy to transport, high-level adjustable. In the cantilever to increase the steel or wooden partitions, suitable for small space, low warehouse, high space utilization, access to goods more convenient and quick, the storage of goods at a glance, compared with the ordinary partition, The higher the cost, for storing bulky, scattered or other special products, cantilevered shelves is the ideal solution.
Cantilever Rack Design:
1. The column is made of two cold-rolled C-type profiles - face-to-face welding, making full use of the material's anti-load capacity, light weight, strong bearing capacity, low cost, more economical and beautiful. Structure formation;
2. The column has a double row of holes, the hole pitch is 140 (50) mm, so the cantilever hanging on it can be adjusted up and down the layers of each layer, increasing the flexibility of storage activities;
3. Design back to increase the overall stability of the shelf, with high-strength cantilever, load capacity, space utilization is high, plus the partition, especially for small space, low warehouse, easy management, broad vision.
Cantilever Rack Features:
1. Cantilevered shelves with structural stability, good load capacity, high space utilization;
2. Cantilevered shelves to increase the partition, suitable for small space, low degree of the Treasury, easy management, wide field of vision, compared with the ordinary partition shelves, the higher utilization;
3. Cargo access by forklift, driving or manual, to facilitate access to the goods.
4 Things to Think About When Buying Pallet Racking
Sturdy, space efficient and easy to navigate.
Optimise Space For Storage
It is important to keep abreast of new ways to improve your business.
Get the Most Out of Your Warehouse
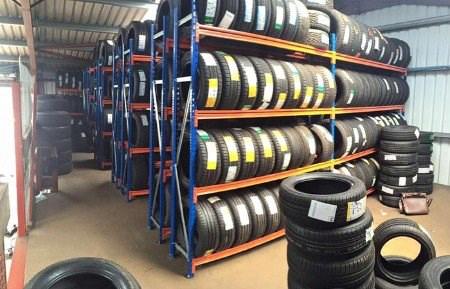
Sturdy, space efficient and easy to navigate.
It’s little wonder that pallet racking systems have become one of the most popular storage solutions for companies across just about every sector.
If you’re thinking about investing in pallet racking, it’s important to take a moment to consider the specific needs of your business, as this will have a big influence on the design and installation of your storage solution.
Not sure where to start? We’re here to help. We know exactly what it takes to create quality pallet racking systems that stand the test of time. Here are a few things to consider:
1. How Much Space is Available?
Perhaps the most important thing to consider when purchasing pallet racking is to have a thorough understanding of the area in which you’re planning to install it. You’ll need to take into account the height, width and accessibility of the area in order to make the most efficient use of the space. A custom made pallet racking system that’s tailored to the exact dimensions of your space can do wonders for maximising storage density, which is essential if space is at a premium.
2. How Are You Going to Access the Racks?
Another key factor to think about is how you’re going to access the racks - particularly those that are elevated. If you stock even moderately heavy goods, there’s a very good chance that you’re going to be using some sort of lift truck to access your inventory, which may dictate which type of racking system is suitable for your space. This also means you’ll need to ensure your lift trucks have safe, unobstructed access to the area.
3. What is Your Budget?
It goes without saying that budget will have a large influence on the type, size and sophistication of your pallet racking system, so put some time aside to establish how much you can reasonably afford to spend. It’s also worth remembering that an effective storage solution can have a dramatic impact on efficiency and productivity across many levels of the business, which essentially enables you to get a better return on your investment. Here at Planned Storage, we pride ourselves on providing quality storage at an affordable price, so be sure to have a chat with a member of our team to discuss your options.
4. How Can You Maximise Safety?
Last but certainly not least, it’s critical that you think about what you can do to ensure your pallet racking system is sturdy, safe and ready to withstand the knocks of day to day life. With this in mind, be sure to always use a trusted and reputable provider to design and install your storage system, and carry out regular maintenance on it. An expert provider will have the resources and specialist expertise required to implement a pallet racking system that minimises the risk of user injury.
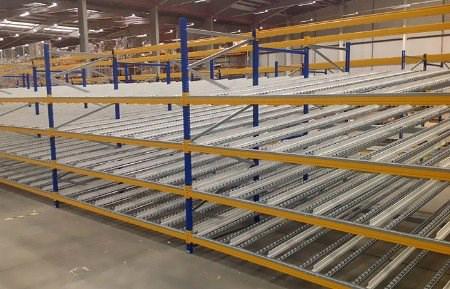
It is important to keep abreast of new ways to improve your business.
In this fast-paced world that continues to grow every minute every day, it is important to keep abreast of new ways to improve your business. This is also about optimising the resources you have at hand. Given the unpredictability of the economy, you may experience a rapid boost in your sales but not enough warehouse space to accommodate the expansion. Initially, you might consider relocating to a larger warehouse to accommodate your needs, but this could provide a bump in the road at a later date. But one way you can make a smart change is optimising your current space. Ever visited a huge furniture warehouse and strolled through aisles lined with pallet racks? Other than acting as a smart storage facility, the pallet racking system makes items easily accessible and this is why it’s successful. Save thousands of dollars by maximising the space that you already have and in doing so enhance workplace safety, productivity and practicality.
Create a spacious workplace - maximise space
The warehouse stocks all the supplies we need for work, but are you stockpiling too much? Look at your inventory – is one product ordered less than others? Then reduce the amount you keep just in case. By streamlining your products in this way, you will allow for more space on the products you need to keep more of, simply by reducing the ones you use less of. Also look at the equipment you’re using, is it old or bulky? Where is it being stored? Is there an alternative space to store it, perhaps a shed can be built on the outside of the warehouse to safely store these items and free up space within the warehouse itself.
Discover new storage solutions, discover space
Make the most of your space with different methods of storage. Here are a few:
Pallet racking: With pallet racking, you can bolster the practicality of just about any warehouse regardless of its size. You can have pallet racks in with aisles wide enough to accommodate vehicles or need a few extra, multi-level storage solutions to keep your products secure. Simply put, no matter your needs, pallet racks have you covered.
Shelving: With metal shelving, you can keep your warehouse tidy and orderly at all times, allowing your workforce to remain productive.
Mezzanine Floor: You can save time, effort and money by maximising the practicality of your existing warehouse, and one of the best ways to utilise currently unused space is to install a mezzanine floor.
Locker: Whether for an educational or commercial setting, locker storage is an excellent way of assuring your r employees that they can keep their possessions and equipment locked away safely. Metal lockers can also double up as hardwearing storage cupboards.
Small parts storage: If your business works with small parts on a day-to-day basis, it’s vital to organise them efficiently. There is a wide choice of small parts storage solutions, such as tilt boxes and wire storage baskets, which can be suited to an array of different working environments.
Let Planned Storage take care of your storage needs
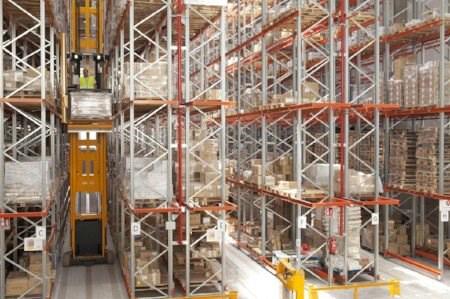
Make plans for your future
With warehouse space at a premium and storage units not always the answer in a busy working environment, you may need to think about reorganising your company’s warehouse. Summer can be a great time to look at inventory, depending on your business but you may find it tiresome to plan a storage strategy and become overwhelmed when you think of pallet racking and shelving. However, making the most of your space can save you money in the long run and even a few inexpensive changes can make life easier for everyone in the warehouse. Planned Storage Ltd have bring you a number of tips to optimise your warehouse storage space:
When you sit down to make a strategy or plan any changes to your warehouse, constantly keep in mind that the space needs to be efficient, profitable and easy to work with. If you plan to install any new technology or storage units, ensure that they are build to last and will meet any future requirements you may have, particularly over the next five years. You need reliable storage solutions that can remain flexible as your business expands. You may need to add space at some point, and if this is in the form of an extension to your current premises, consider how the current shelving may affect that.
Throw out the old
If you have old technology or shelving that keeps causing you problems, then it’s costing you time and money operationally. It’s better to invest now in new pallet racking so that your business can continue to grow. Also consider if anything old is blocking your space? Some old doors take up far more space than new ones, especially in older warehouses. Many door systems have bulky rails in the ceiling or over the doorway. These can be replaced and you’d be amazed how much space they free up. Modern shutters are secure, fold easily and are much more compact, so you can utilise the extra space. This is also true of old lighting, electrics etc.
Reconsider your warehouse layout
Decide if the layout of your warehouse is working for you. Are your shelving units easily accessed by forklifts or other machinery? Do you need additional shelving for one particular product? Are you shelves at a safe height for the safety of your employees? Before you decide to make any extensive structural changes, it’s important to consider all the factors.
Install vertical storage
Once you’ve had a look at the overall layout, you may see that there is space that can be utilised better, especially vertically. Figure out how much space you think you have to work with and talk to the experts at Planned Storage to come up with some storage solutions that can help you.
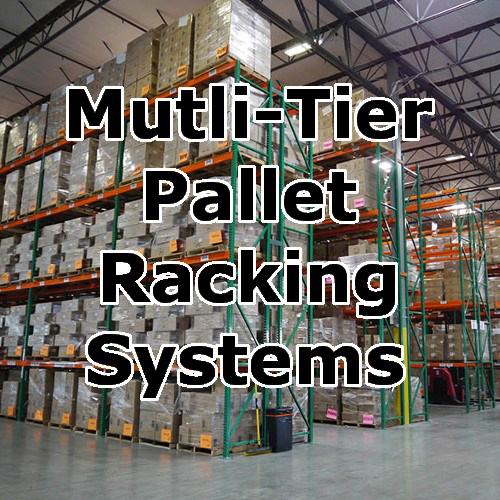
Improve Your Warehouse Space And Operational Capability.
IF YOU ARE STRUGGLING WITH FLOOR SPACE, THE ANSWER IS TO GO UP!!
Multi-tier racking systems are a solution for businesses looking to maximise their storage area. The large steel structure of a multi-tier system may seem financially daunting, but this solution is much more cost effective than warehouse expansion or relocation, which could impact on business productivity.
The system is specifically designed to suit businesses running a picking operation with a number of SKU’s (stock keeping units) – online retailers and e-commerce operations benefit highly from the multi-tier racking solution. The system is extremely flexible giving the option of any number of levels and accessories required to suit the business’s needs. With the growth of online shopping, the need for more space is only going to become a bigger issue for businesses in the future.
Depending on your requirements, the warehouse design will incorporate the need for pallet tucks and trolleys – ensuring maximum space is provided to create an easy picking environment but also effectively use the space within the warehouse so efficiency is optimised and warehouse productivity can be maximised.
It is important to remember that you cannot store flammable products such as: aerosols, explosives or fireworks as per the Building and Safety Regulations within a multi-tier racking system.
Benefits of a multi-tier racking system:
Provides huge increases in storage capacity (in some cases up to 100%)
Allows for simultaneous order picking
Increased floor space is gained for storage, packing and assembly needs
It is also possible to add the following accessories to improve the systems functionality:
Goods lift, pallet gates, gravity chutes (for transferring products from level to level)
Improved flooring – galvanised steel / timber decking
Safety options – protective handrails / mesh netting
Interested in finding out more? Complete the contact form and a member of the team will get back to you or give us a call today.
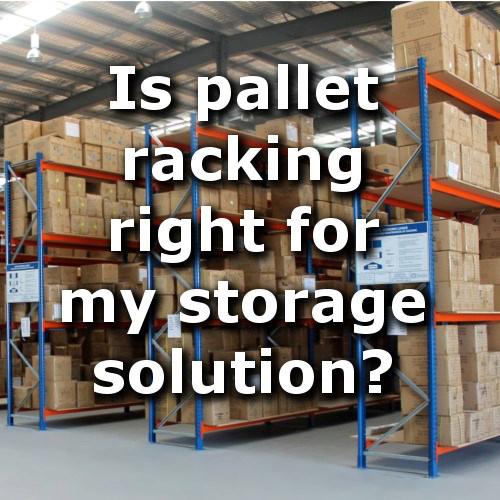
Pallet racking
Pallet racking is one of many choices when it comes to utilising the space in your current warehouse or commercial property. We are frequently approached to help advise on the best solution for storage issues, things you need to consider are:
The products you store
How you store them
How accessible these products need to be and how they are accessed.
We have put together a short list of questions that we are often asked when it comes to making the decision to have pallet racking installed.
Who needs pallet racking?
Anyone who needs to handle bulk products (on a pallet) and wants to best utilise the space by not block stacking.
What are the advantages of pallet racking over block stacking?
There are multiple advantages:
Ease of moving individual stock, so pallets are not sat on top of each other
Product does not get damaged and crushed from pallets above
Maximises height so there is no dead space above
What sort of handling equipment do I need?
This is the million dollar question! There are lots of different options available to you, the answer is very much dependent upon your budget, pick criteria and the size of your warehouse.
How can I decide?
We can offer straight forward and sensible advice to best suit your needs, we will even be able to offer some impartial advice on the type of truck that would suit your requirements (we do not sell them)
Will you manage the whole project?
Yes, we manage the project all the way through from initiating the concept, arranging dates and installation crews (plus any plant needed) to completion of your project. Budget and timescales will be discussed and we will ensure we deliver to your expectations.
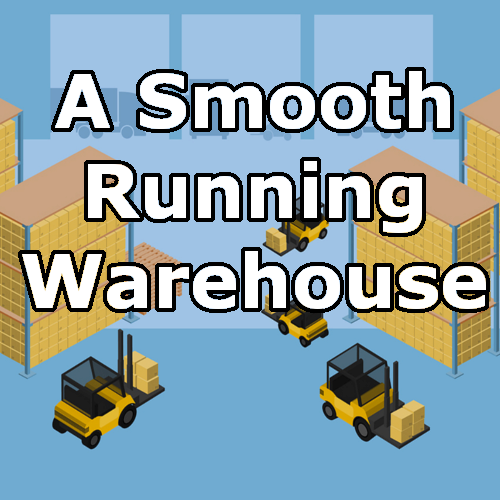
Maintaining a smooth running warehouse can be a challenge!
Here we explore a vast range of tips from receiving goods to using the correct lighting to ensure your warehouse runs in complete sync with your workforce:
ORGANISATION IS KEY
If you want to make the most of your time, it’s important to consider keeping your fastest moving materials front and centre. Cleverly grouping these products will allow your workforce to pick and pack more efficiently. Think of a supermarket. If you’re looking for biscuits you wouldn’t visit the fruit aisle!
RECEIVE WITH CAUTION
When materials and stock arrives at your warehouse, be sure to inspect thoroughly. You might have the strongest relationship in the world with your supplier, but at the end of the day if there’s an issue when the product reaches the customer- it’s down to you!
APPLY A LOGICAL PICKING PROCESS
If your organisation tends to ship a small number of orders against a high quantity of products, it’s a good idea to devise a rotation-style list so that the picker doesn’t find himself in a back-and-forth battle. Similarly, if you ship a large number of small orders, try to organise lists by product groups then process to distribute each product by customer order number when it reaches the verification stage.
REORGANISE WHEN NECESSARY
Today’s every changing trends will require you to meet different needs often and the items that were popular last month, may have been taken over by something completely different this month. This is why it’s important to reorganise your inventory and warehouse storage systems on a regular basis. Change the space you use to allocate these materials to give pickers easier access to the most popular items.
PRACTICE EFFICIENT QUALITY CONTROL
In any busy warehouse environment there will always be cases where faulty or wrong products are picked. In order to avoid a build-up of these unwanted items it’s important to have a dedicated storage area and a rota for returning the items to their correct places.
SAFETY FIRST
Operating a safe environment is critical. Accidents can cost you the employees you need to keep your business running. Make sure that you are meeting all of the enforceable health and safety requirements for your industry. Avoid slips, trips and falls by ensuring there are no loose materials, liquids, unnecessary steps, boxes or dark areas on the floor. Dispose of worn and exposed wires, lock up flammable liquids and run electrical cords under the flooring to reduce the risk of fire.
TRAINING MATTERS
It can seem tedious, and often leave employees feeling underwhelmed. But in the case of an accident, training can potentially save lives. Be sure to educate your employees- the best way to avoid accidents in the workplace is to properly train your workforce to prevent and deal with accidents. Always have a first-aider on site. Schedule refresher training to keep employees up to speed on the newest policies/procedures in the industry.
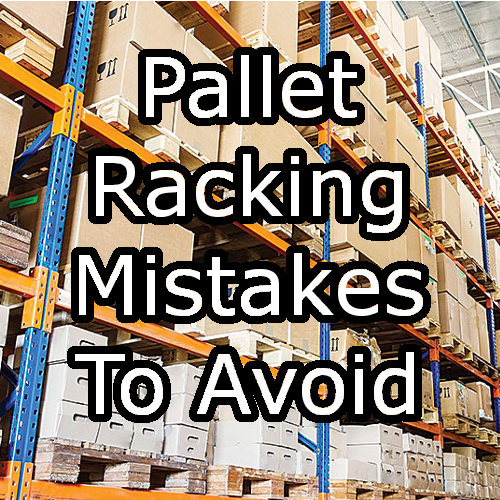
Six common mistakes!
Visit any type of warehouse, distribution centre or storage facility you can think of and you’ll likely come across some form of pallet racking. Chances are the pallet racking you see will have been carefully designed and chosen to meet the specific needs of that facility, but in some cases, the process is rushed and the wrong system ends up being installed.
We’ve compiled a list of six common mistakes to avoid when it comes to purchasing a racking system:
No.1
CHOOSING THE WRONG SIZE
Without proper guidance it can be easy to choose a system that doesn’t quite fit your premises or isn’t suitable to work in coherence with your equipment or employees. Buying racking that’s too tall for your forklift trucks or a system that is too narrow may end up being completely disregarded and considered as a waste of time, effort and capital. It’s crucial that your dimensions are extremely accurate to avoid any problems with both installation and day-to-day operations.
No.2
NOT TAKING COMPATIBILITY INTO ACCOUNT
It’s easy to assume that one type of racking suits all, but this is simply not the case. The type of racking you choose needs to be carefully considered, especially where storing awkward items is concerned. Some racking is universally designed, other systems are only compatible with products from the same brand. We recommend choosing a universal design that can cope with changing stock and demands and will save you time and money in the long run.
No.3
BUYING ONLY WHAT YOU NEED
Contrary to popular belief, less isn’t always more. This is especially the case when talking about warehouse storage systems with regards to both costs and space. Efficient purchasing in this case involves investing a little extra to cater for any sudden need for additional storage. The trick is to not only consider what your business needs in the present, but what it may need when looking to the future.
No.4
BUYING USED RACKING ON IMPULSE
Used racking is pretty easy to come across, and it’s usually considerably cheaper than a new system. With this in mind, it’s important to ensure that the used racking you invest in is of the best quality. The surface appearance of racking and accessories can be deceiving, and sometimes hides a plethora of underlying problems and potential hazards. If you’ve decided to go down the route of purchasing used pallet racking, ensure you buy from a reputable specialist who can advise on whether or not it’s going to be suitable for your establishment and operations. We, however, always advise buying from new, for peace of mind.
No.5
OVERLOOKING DAMAGE
It only takes one search on YouTube for ‘Pallet Racking Disasters‘to make you realise the potential risks of installing or continuing to operate a damaged system. It’s incredibly important to have your racking inspected regularly by a professional, carry out extensive training amongst forklift drivers and invest in quality systems to ensure these types of disasters are avoided.
No.6
PURCHASING THE CHEAPEST OPTION
There’s a common saying ‘buy cheap, buy twice’ that’s especially fitting when it comes to warehouse storage systems. Choosing the cheapest pallet racking system you can find may prove damaging to you, your business and your staff. Take the time to shop around and invest in racking that’s compatible with your requirements, reliable and strong to avoid additional costs in the future.
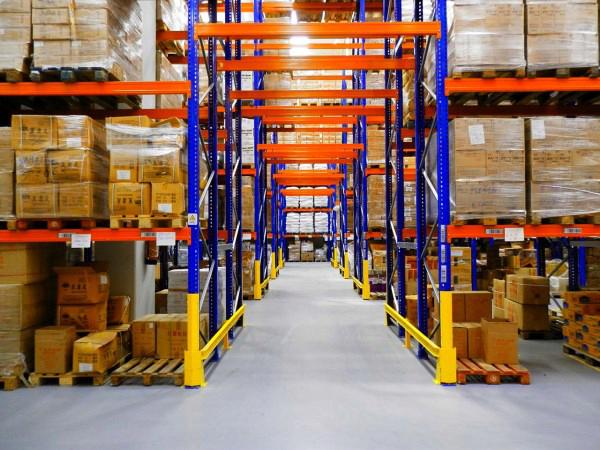
Storage systems
The racking system in warehouses serves as the heart of operations. When choosing your storage system, the primary consideration focuses on the suitability of application and the ability to maximise the available space while facilitating productivity.
Exploring All Warehouse Shelving Options
The first step is to examine your warehouse and determine whether racking or shelving is primarily needed. If your warehouse has a large area, stores large goods and has a high product flow, industrial warehouse racking systems may be the most efficient storage option.
Next, identify which combination of rack styles is the most suitable for your warehouse. Industrial warehouse racking does not have to be limited to one size or type. Exploring all your options is the best way to customise your warehouse in order to maximise the available space.
Selective Pallet and Drive-in Racking
If your warehouse has a continuous product circulation, consider selective pallet racking. This racking system allows you to access all palletised goods simultaneously, leading to increased productivity in your operations. With selective racking, pallets are unloaded and loaded from the front of the racking system.
For warehouses that hold large quantities of homogeneous products, the drive-in rack is the most suitable for use. For drive-in racks, forklifts load and unload goods by entering through the front of the system and then backing out once all goods are in place. Drive-in racks follow the last-in, first-out inventory management, so it’s necessary that the goods placed last in the system will be the items retrieved or transported first.
Cantilever and Push Back Racking
Cantilever racking is ideal for easy retrieval and storage of products with different lengths, weights and sizes. Without the requirement for uprights, these systems allow easy access and selection of goods with high down-aisle density. Cantilever racks offer easy arm adjustability that provides a wide range of capabilities that can be customised to your preference.
Consider push back racking systems if your warehouse requires access to several stock-keeping units simultaneously. Similar to drive-in racking, push back racks are designed for last-in, first-out inventory management. As a high-density storage solution, push back systems are designed to maximise storage capacity.
Long Span Shelving
If you are looking for a shelving system, long span shelving is a suitable option for a wide range of applications. This clip-together shelving system is ideal for storing small tools and heavy, bulky materials. Since they are assembled using an easy clip-together system, their shelves are fully adjustable and can be used to support a mezzanine floor system. Their versatile features allow the addition of accessories, such as security cages, crates, tool racks and more.
Industrial Warehouse Storage Systems by Storeplan
Storeplan offers all these racking and shelving systems in its collection of warehouse storage solutions. Our racks and shelves not only accommodate the storage needs of industrial warehouses, but they also cater for the medical, automobile, mining and transport sector.
If you need assistance in selecting the best storage solution for your warehouse, do not hesitate to call 1300 551 281 or send us a message through our contact page.